Top 8 Data Science Use Cases in Manufacturing
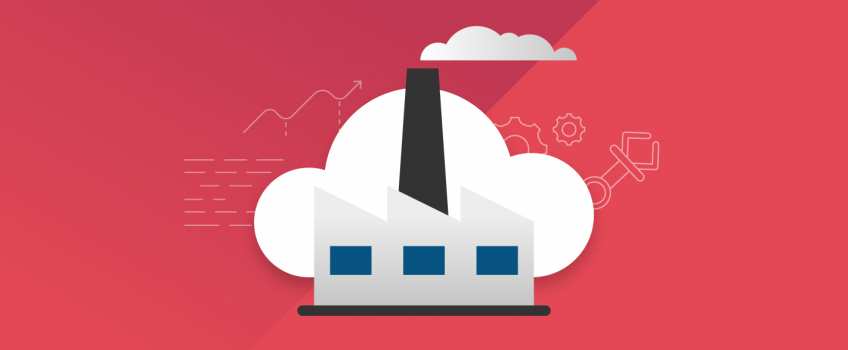
The manufacturing business faces huge transformations nowadays. Due to rapid development of digital world and broad application of data science, various fields of human activity seek improvement. Modern manufacturing is often referred to as industry 4.0 that is the manufacturing under conditions of the fourth industrial revolution that has brought robotization, automation and broad application of data.
The amount of data to be stored and processed is growing every day. Therefore, today's manufacturing companies need to find new solutions and use cases for this data. Of course, data brings its benefits to manufacturing companies as it allows to automate large-scale processes and speed up execution time.
Data science is said to change the manufacturing industry dramatically. Let's take under consideration several data science use cases in manufacturing that have already become common and brought benefits to the manufacturers.
Predictive analytics
Predictive analytics is the analysis of present data to forecast and avoid problematic situations in advance. Manufacturers are deeply interested in monitoring the company functioning and its high performance. Finding the best possible way to hold problematic issues, overcoming difficulties or preventing them from happening at all are marvelous opportunities for the manufacturers using predictive analytics. The implementation of predictive analytics allows dealing with waste (overproduction, idle time, logistics, inventory, etc.). Therefore, let's concentrate on the possible solutions brought by predictive analytics.
Fault prediction and preventive maintenance
Both these prediction models are aimed at forecasting the moment when the equipment fails to perform the task. As a result, the secondary goal may be achieved - to prevent these failures from happening or at least to reduce their number. This becomes possible due to the numerous predictive techniques.
Preventive maintenance is usually applied to the piece of equipment that is still working to lessen the likelihood of its failing. There are 2 major types of preventive maintenance: time-based and usage-based. The biggest strength of preventive maintenance is planning. Having at hand the prediction concerning future troubles with the equipment, the manufacturer may plan a break or a shut down for repairing. Such breaks are usually made to avoid considerable delays and failures, which are often caused by more significant problems that may arise.
Demand forecasting and inventory management
Demand forecasting is a complex process involving analysis of data and massive work of the accountants and specialists. Moreover, it appears to have strong relations with inventory management. A simple fact may explain this interrelation - demand forecasting uses the data of the supply chain.
There are a lot of benefits of demand forecasting for the manufacturers. First of all, it gives the opportunity to control inventory better and reduce the need to store significant amounts of useless products. Besides, the online inventory management software helps to collect data that may be of great use for further analysis. One more critical factor is that the data input for the demand forecasting may be continually updated. Thus, relevant forecasts may be made. Additional benefits lie in the improvement of the supplier-manufacturer relations, as both can efficiently regulate their stocks and supply process.
Demand forecasting and inventory management take into account numerous factors, among which are external factors like the economy or markets, raw material availability, etc. In this way, you can get a more complex view of your manufacturing business performance and further planning.
Price optimization
Manufacturing and selling the product involves taking into account numerous factors and criteria influencing the product price. All the elements starting with the initial price of the raw material and up to the distribution costs contribute in the final product price. And what happens when the customer finds this price too high or too low?
Price optimization is the process of finding the best possible price both for manufacturer and customer, not too high and not to low. Modern price optimization solutions can increase your profit efficiently. These tools aggregate and analyze pricing and cost data both from the internal sources and those of your competitors and derive optimized price variants.
Under conditions of highly-competitive market and changes in customers’ needs, price optimization becomes a must and grows into a continuous process.
Warranty analysis
The manufacturers spend a considerable amount of money every year on supporting warranty claims. Warranty claims disclose valuable information on the quality and reliability of the product. They help to reveal early warnings or defects of the product.
Using this data, the manufacturer can make improvements to the existing products or develop new ones, more effective and efficient. Modern warranty analytics solutions help manufacturers to process vast volumes of warranty-related data from various sources and to apply this knowledge to discover where the warranty issues are rising and the reasons for their occurrence.
Robotization
Robots are changing the face of manufacturing. Nowadays, it is a common cause to utilize robots for performing routine tasks, and those which may be difficult or dangerous for people.
The manufacturers tend to invest more and more money into robotization of their enterprises every year. The AI-powered robot models help to satisfy the ever-increasing demand. Moreover, industrial robots largely contribute to increasing of quality of a product. Every year, the upgraded models come to the production floor to revolutionize the production lines. They are straightforward. Moreover, manufacturing robots are more affordable for enterprises than ever before.
Product development
Big Data has brought big opportunities to manufacturing companies regarding product development. The manufacturers use the advantage of Big Data to understand their customers better, to meet the demand and to satisfy their needs. Thus, data may be used to develop new products or to improve the existing ones.
Using Big Data for product development, the manufacturers can design a product with increased customer value and minimize the risks connected to introduction of a new product to the market. Actionable insights are taken into account while modeling and planning. This data can strengthen the decision-making process. Also, data management tools are widely applied to optimize the operational aspects of the distribution chain.
Processing customer feedback and feeding this data to product marketers may contribute to the idea generation stage. Thus, a new product which would prove more useful to the customers and more profitable for the manufacturers may be developed.
Computer vision applications
AI-powered technologies and computer vision applications found their usage in manufacturing at the stage of quality control. In this respect object identification and object detection and classification proved to be very efficient. Usually, quality control monitoring was performed by people. However, now it is more common to rely on computer vision rather than on human vision. These monitoring systems usually consist of computer hardware and software, cameras, and lighting for image capturing. After that, these images are algorithmically compared to the standards to identify discrepancies.
Among key advantages of the computer visions applications are:
- improved high-quality control
- decrease in labor cost
- high-speed processing capability
- continuous operability 24/7.
Managing supply chain risk
Supply chains have always been complex and unpredictable. Risk has always been a part of the manufacturing processes and product delivery. Using big data analytics for managing supply chain risk may be quite beneficial for the manufacturers. With the help of analytics, the companies can predict potential delays and calculate probabilities of the problematic issues. The companies use analytics to identify backup suppliers and develop contingency plans.
To keep a pace of the continuously changing tendencies the application of the real-time data analytics is essential. Prediction and management of the possible risk are crucial for the operation of a successful manufacturing business.
Conclusion
The area of manufacturing is undertaking considerable changes due to the development of technologies and the appearance of ML and AI solutions. This article provides several most vivid examples of data science use cases in manufacturing together with the benefits they bring to businesspeople.
Along with forecasting possible risks, demand and the requirements of the market, data analytics can help to keep up with high-quality standards and quality metrics. Moreover, incorporating smart data techniques into manufacturing may help to forecast unexpected wastes or problems. Big data can help to achieve many of the business goals set by the manufacturers having spending less time and money as ever before.
Comments
Add a new comment: